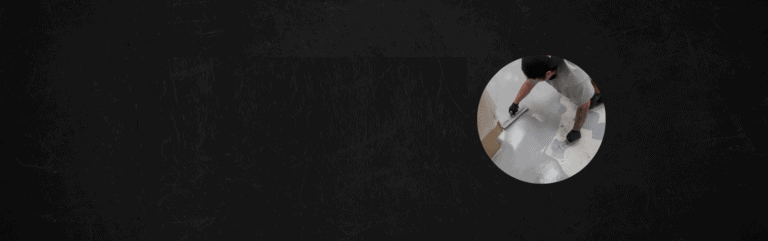
CHOOSING A FLOORING TOP COAT (EPOXY vs POLYASPARTIC vs URETHANE)
When working with the variety of floor top coating solutions that are on the market, it should be understood that every coat you install from primer to basecoat and topcoat, plays an important role in your floor’s overall performance. In this article, our Columbus Epoxy Flooring team will discuss how