You hear companies talk about those DIY epoxy kits, to stay away from them, and that they all fail. At Columbus Epoxy Flooring we agree with them completely, but why exactly are these DIY kits a bad option and what causes them to fail?
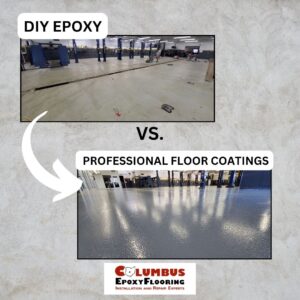
The low cost of the DIY option is appealing but as with most decisions in life, price isn’t everything and floor coatings are no exception. To start off, the epoxy coatings you find in the big box stores are a water based epoxy with only a 50% solids content and perform more like a paint. In the coatings world, solids content can help to determine the strength of the coating as well as the final thickness. When coatings are applied the thickness is measured using WFT (wet film thickness) and DFT (dry film thickness). To help understand further, the DIY kits specify that you apply the coating at around 7-8mils (1 mil= 1000th of an inch). 7-8mils is the WFT (wet film thickness). These coatings however, are only 50% solids, meaning 50% of the applied thickness will evaporate, leaving a final DFT (dry film thickness) around 3.5-4 mils. Professionals prefer to use 100% epoxy for the strength and the high solids content. These coatings are applied around 12-16 mils per coat to create a much thicker and stronger surface for the final outcome.
Thickness and higher solids content is only one reason industrial grade epoxies and other coatings are stronger. The coatings professional use also contain additives along with different chemistries all together which allows them to hold up against harsh chemicals, impact from heavy objects, daily abrasion, and provide protection from UV light. It’s also important to understand that not all coatings are created equal. In the professional floor coatings space we must use a variety of different coatings such as; polyureas, polyaspartics, 100% solids epoxies, water based epoxies, aliphatic and water based urethanes, novalac epoxies, MMA (Methyl Methacrylate) and many more. All these different chemistries are designed and engineered for their own purpose, and understanding why these coatings should be used for different purposes helps installers to provide the optimal solution that is right for our client. Part of our process to help find the right coating solution includes asking a number of questions to help determine what chemicals will be used on the floor, what daily traffic the floor will experience, how much downtime is allowed for the installation process that includes curing schedule after the floor has been installed.
The difference in chemistry of industrial coatings vs DIY is only part of why DIY coatings fail. Proper floor preparation contributes largely to the success of an installation and is the most important part for all coating applications. Epoxy coatings that are designed to be applied at a thickness around 4-40 mils must be prepped leaving a CSP (Concrete surface profile) of 3-5. A CSP of 3-5 can be achieved by diamond grinding or shotblasting. Many DIY epoxy kits recommend acid etching to clean the concrete and create a porous textured surface. Acid etching can generally only achieve a CSP 1. Acid etching can also leave an acidic residue behind and if not properly cleaned will further weaken the bond of the coating to the surface. Regardless of preparation method, a thorough cleaning of the floor is also required to remove any loose dust and other debris that may affect the bond of the coatings to the concrete surface.
All epoxy coatings are designed to be applied a certain way and any incorrect method may also cause failure of the project. Because DIY epoxy kits are generally 50% solids they must only be applied at a certain thickness. The thickness specified is only 3.5-4 mils or 250 square feet per mixed gallon. If these floor coatings are applied much thicker, any solvent that is contained within the epoxy will be unable to evaporate causing the coating to foam and ultimately fail. When working with any coatings you must be familiar with technical data and thoroughly understand how the coating should be applied to assure a successful installation.
Conclusion
Our professional Team has spoken with many people who attempted a DIY epoxy coating projects only to experience a lot of wasted money, headaches, frustration, and see all their hard work fail in a matter of months. We want to make sure all of our clients don’t have to experience these frustrations when looking to have a floor coating installed. Our team is trained and thoroughly understands how to successfully install resinous flooring to provide a solution that is right for our clients. If you have any questions or would like us to look at a potential project for you, please give a call at 614-470-2649 and we’ll be happy to help!
References:
DIY epoxy application method and thickness.
https://www.rustoleum.com/-/media/DA74ED5C0FAC47AEAD3074F3522BA4CA.ashx
Why to not acid etch.
https://www.dur-a-flex.com/tech-tips/avoid-preparing-concrete-with-acid-etching/
About CSP (concrete surface profile).
https://www.runyonsurfaceprep.com/how-rough-should-my-concrete-surface-be-for-a-proper-coating/
https://www.tccmaterials.com/wp-content/uploads/2020/06/ConcreteSurfaceProfiles.pdf